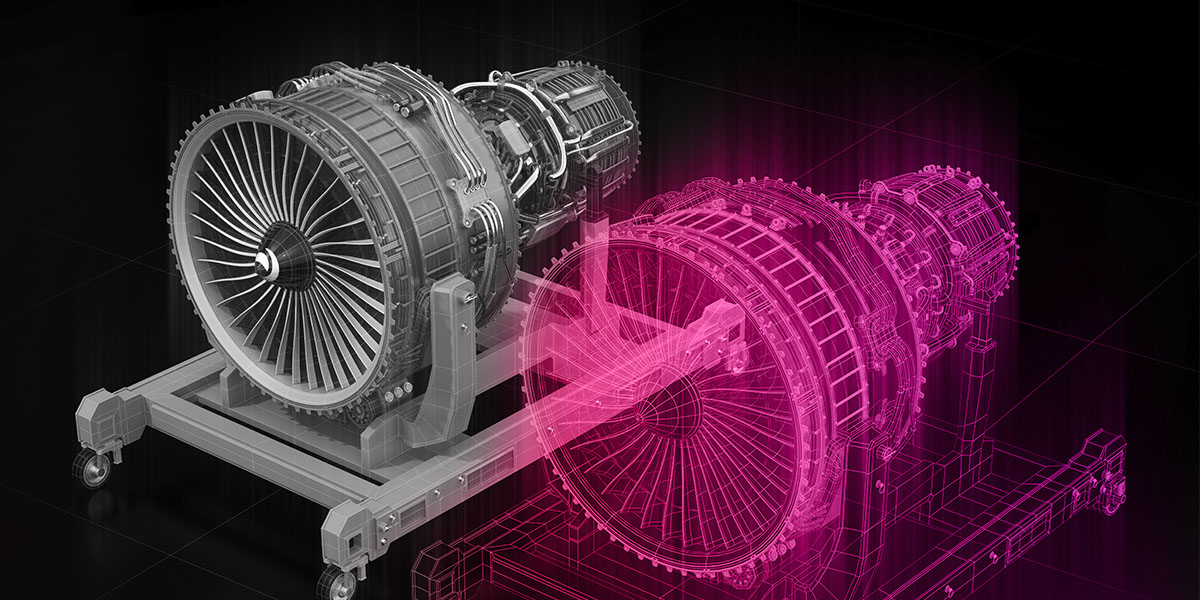
The manufacturing industry can leverage digital twins to understand operations better and optimize processes. With greater insight into your systems and equipment from these cutting-edge digital technologies, your team can effectively drive efficiency and innovation to stay competitive.
Explore how digital twins can benefit your manufacturing operations and drive future growth.
What Is a Digital Twin in Manufacturing?
A digital twin in manufacturing refers to a virtual replica of physical assets, systems, or processes informed by Internet of Things (IoT) sensors. This twin functions as a virtual representation of one of your machines, production lines, or products by mimicking its real-world behavior. You can use this digital technology to simulate different scenarios and analyze performance for more informed decision-making and monitoring.
Digital twin technology is commonly confused with simulations, but the two differ. A simulation typically relies on a computer-aided design system or similar solution to forecast how physical assets will work or behave. Digital models use IoT data collected from your specific equipment and systems.
The Role of Digital Twins in Manufacturing
The manufacturing industry’s use of these virtual models is among the most advanced of any sector. Some common digital twin applications for industrial production include:
- Design and development: Manufacturers use these solutions to create digital prototypes of their production systems on products. Digital twins offer a low-stakes way to test configurations, identify potential hurdles, and optimize performance before production.
- Performance monitoring: Digital models enable teams to monitor assets and system processes continuously. The data collected from IoT sensors can track key performance indicators, flag inefficiencies, and make proactive adjustments to support efficiency.
- Quality control: Manufacturing plants leverage digital twins to compare real-time data with the virtual model to detect potential deviations and bottlenecks early, enabling early intervention to ensure consistent quality standards.
- Training and simulations: Digital twins can also function as simulations for training manufacturing personnel on new equipment and production processes in a safe and risk-free virtual environment. Operators can use this digital technology to undergo training and practice to prepare for real-world scenarios.
- Lifecycle management: Businesses can leverage these digital tools to gain insight into each stage of a product or system, from design to production. Manufacturers can use the insights from digital twins to optimize lifecycles and enhance overall quality.
7 Benefits of Digital Twin Technology
Explore the key digital twin benefits for manufacturing operations below.
1. Predictive Maintenance
Manufacturers can leverage digital models to enhance equipment and production reliability through data-driven predictive maintenance. Real-time data from the sensors can predict when a breakdown is likely to occur. By flagging issues and inefficiencies early, your team can stay on top of upkeep to ensure asset performance and productivity. Your personnel can use virtual replicas to proactively identify and address repair needs before they result in costly unplanned downtime or equipment replacements.
2. Process Optimization
Digital twins can facilitate manufacturing process optimization by giving your team a virtual representation of your operations to simulate different scenarios. You can use these insights to identify bottlenecks and opportunities for improvement.
Manufacturers use these solutions to refine their production processes at every level, ensuring optimal workflow design. Fine-tuning processes based on digital twin insights can help industrial production personnel reduce lead times, support better performance, and achieve higher productivity.
3. Cost Reduction
A huge advantage of digital twins is reducing costs by informing optimized maintenance schedules, minimizing unplanned downtime, and reducing the time and expenses associated with operator training. Your manufacturing operation can use the insights from digital models to use resources more efficiently and reduce waste. These technologies can also improve profitability for manufacturers by informing decision-making.
4. Real-Time Monitoring
Live data tracking capabilities from IoT sensors inform virtual models and enable businesses to quickly identify trends and problematic operations. These robust insights are integral to timely interventions and quality assurance measures.
The continuous stream of real-time data is key to efficiently responding to anomalies before failures occur, helping manufacturers support the smoothest operations.
5. Product Innovation
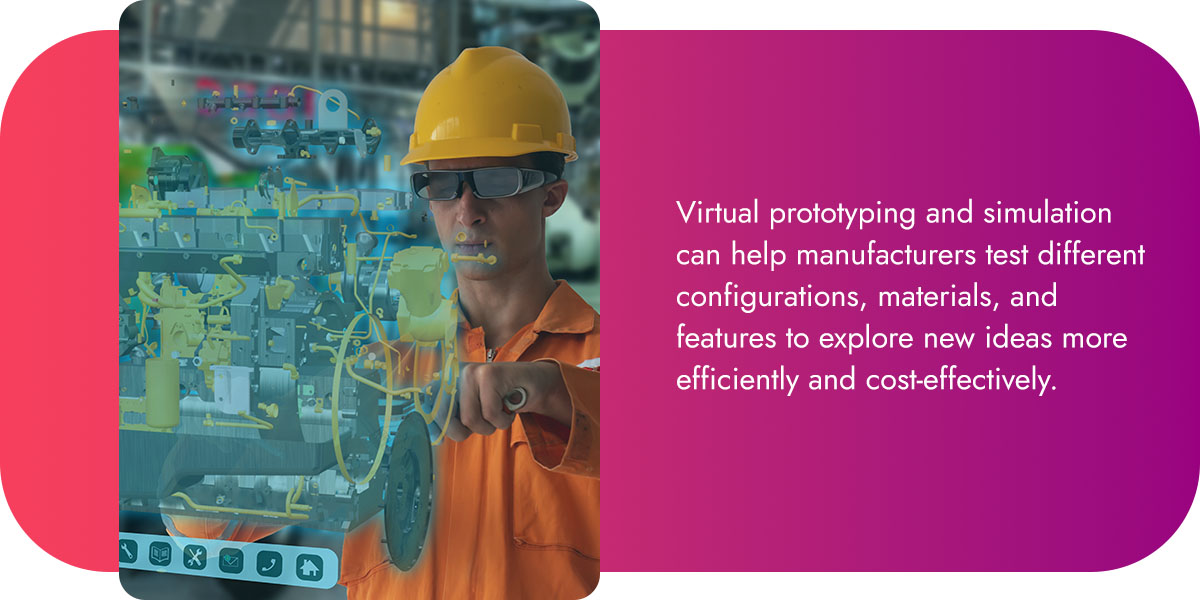
Digital twin technology can help businesses drive product innovation. Virtual prototyping and simulation can help manufacturers test different configurations, materials, and features to explore new ideas more efficiently and cost-effectively.
Digital models can help you bring innovative products to market or implement optimized processes faster, giving your operation a competitive edge.
6. Data-Driven Planning
Another advantage of using these virtual models is having access to real-time data to drive decision-making and support accurate predictions regarding manufacturing operations. Digital twins can guide the following:
- Resource allocation
- Production planning
- Quality control
- Supply chain management
- Opportunities for improvement
Strategic, data-driven planning helps manufacturers mitigate risks and make smarter decisions to drive profitability, sustainability, and longevity.
7. Scalability
The manufacturing industry can also leverage digital twins to swiftly adapt to changing market demands and scale. These tools can easily accommodate increased data volumes as your business introduces new products, production lines, and facilities into its operations. Your team can make informed, data-backed decisions thanks to these tools’ predictive and monitoring capabilities.
Overcoming the Challenges of Adopting Digital Twin Solutions
While utilizing digital twins can be highly advantageous for manufacturers, a few key challenges can impact adoption and implementation:
- Data integration: IoT systems collect data from multiple sources, and differing data formats can complicate integration and interoperability.
- Data quality: The insights that inform digital twins must be accurate, consistent, and reliable. Issues with data quality can result in misleading behavior and negatively impact decision-making.
- Security and privacy: Robust data security measures are necessary for safeguarding intellectual property and combatting cyberthreats.
- Skill gaps: Your team may lack expertise in IoT systems and digital twin technologies, which can slow implementation. Training and ongoing education may be necessary to maximize the benefits of these solutions for your manufacturing business.
Future Trends for Digital Twins in Manufacturing
Digital technology is constantly evolving, and digital twins are no exception. The following are a few future digital twin trends to watch out for in the manufacturing industry.
Edge Computing Adoption
Edge computing can process data locally and in real time, close to the data source, for incredible accuracy. It can offer several benefits to digital twin systems, including reducing latency, improving reliability, and optimizing bandwidth usage.
Extended Reality
Businesses are using augmented reality (AR) and virtual reality (VR) to enhance their use of digital twins. AR and VR allow businesses to provide users with a more immersive and engaging experience when interacting with virtual models. Manufacturers can use AR and VR to assess product viability and enhance testing.
Best Practices for Implementing Digital Twins With IoT
Following a few best practices will help your manufacturing operation maximize the benefits of digital twins and IoT solutions:
- Prioritize data quality: Monitoring and verifying data quality is key to ensuring that the insights from your IoT sensors deliver the most accurate and relevant data for your digital models.
- Implement robust security and privacy measures: Strong data security solutions are essential to protect private information transmitted between your digital twin platform and IoT devices.
- Establish a feedback loop: Encourage users to share feedback about your manufacturing operation’s digital twins to support continuous improvement and inform newer, more accurate virtual model iterations.
JumpStart Your Manufacturing Transformation With Kopius
If you’re ready to enhance your manufacturing operations, turn to Kopius. We’ll help you transform your business with tech-enabled innovation.
With our JumpStart program, you will streamline new manufacturing solutions and fast-track business results to drive long-term growth. Our experts will assist you in tackling your digital manufacturing initiatives and overcoming common challenges through our data-driven approach. We’ll help your operation gain a competitive edge through the latest digital technologies and solutions.
Are you interested in learning more about elevating your business and unlocking your potential? Contact Kopius to JumpStart your smart manufacturing success today.
Related Services:
Additional Resources: